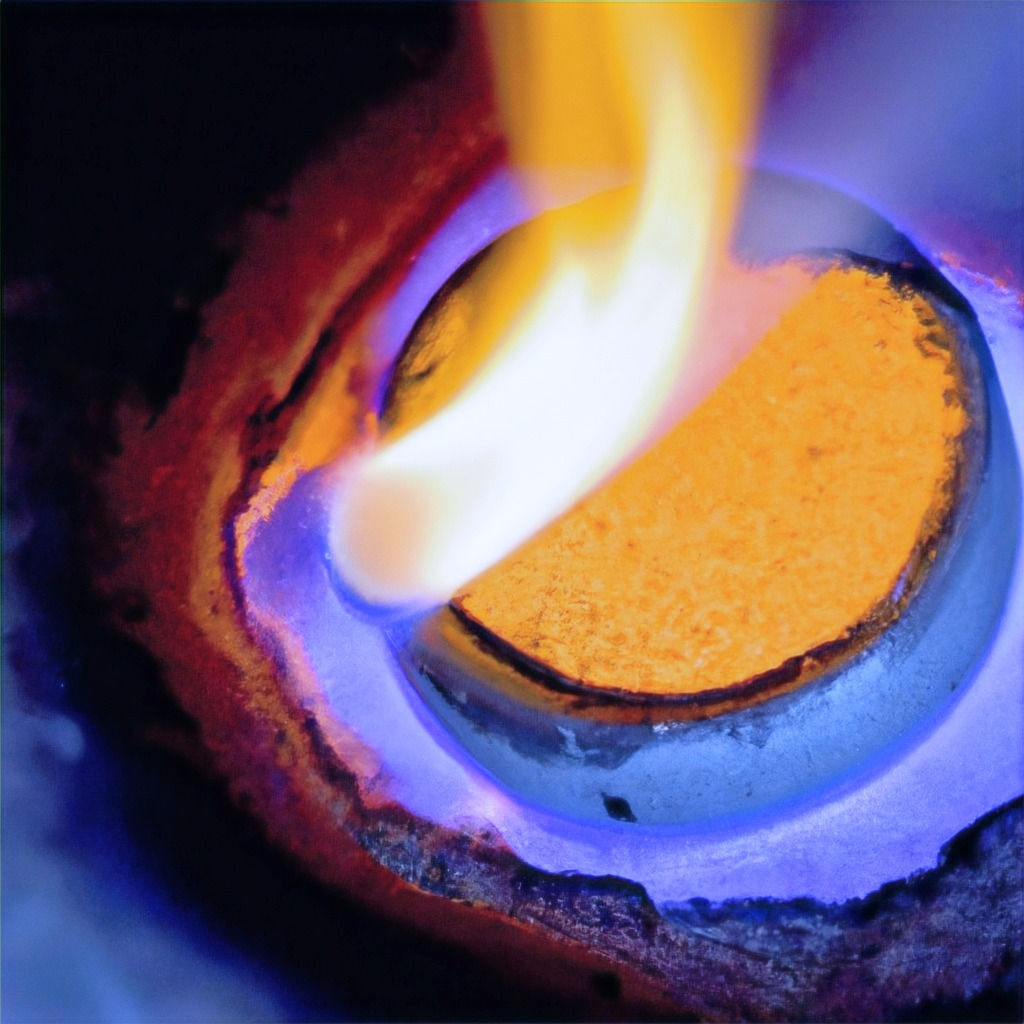

MANNINGS USA
(UK) PLC

ONSITE BOLT INDUCTION SERVICES
CHOOSE INDUCTION WHEN YOU REQUIRE SPEED & QUALITY ON YOUR SIDE
01704 229625
CALL NOW​
E MAIL : info@manningsusa-uk.com

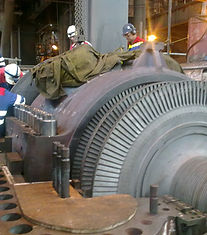


Bolt Heating
At RWENPower Tilbury Power Station Mannings USA (UK) PLC used patented induction heating equipment to safely and speedily remove the massive steel bolts which secure the HP and IP steam turbine covers. The HP turbine has 40 bolts which are each 5 inches in diameter and the turbine had not been opened up for at least four years.
The Turbine Mechanical Engineer at the Tilbury Power Station said “the main advantage to us of using induction heating is the safety aspect. The alternative is to insert a heated carbon rod into the bolt and this rod has to be removed by hand while it is still glowing red hot. Because of the working environment and high temperatures involved we consider this to be extremely dangerous and we welcome this new development”.
Induction Brazing
The use of induction heating is of particular advantage when used on the blades of a turbine and alternators as the heat can be accurately controlled and can be directed to exactly where it is needed. This prevents the blades from overheating and avoids local hot spots which can result in hardening and cracks in the blades.
This proved to be of particular advantage to Dowding & Mills plc who are one of the UK’s major electricity, electronics, mechanical and instrumentation service groups. Dowding & Mills were developing a process for brazing stainless steel de-tuning weights to turbine blades for British Energy at the Heysham 2 Power Station. It was necessary to find a method of carrying out the brazing without removing the blades from the rotor of a turbo-alternator and the work had to be completed within a tight time schedule.
The turbine rotor has 192 blades per row with only a 12mm gap between each blade.
Mannings USA (UK) PLC were invited to propose a suitable means of brazing by means of induction heating and experimentation began to design a coil which would provide adequate heat distribution and control. They produced an induction heating coil which was designed to suit the curvature of the blade and could evenly distribute heat over the small 1½ x 1½ inch area. A thermocouple was attached to the blade and the temperature was raised to 630 degrees centigrade in ten minutes and held at this temperature.
Erosion Shield Removal using Induction
Mannings USA (UK) PLC were able to use induction heating for Innogy Operations and Engineering at their TSG Workshop in Ferrybridge where overhaul of a turbine rotor for the Didcot A Power Station in Oxfordshire involved removal of erosion shields. Geoff Streets, who is Technical Engineer for Innogy said, “induction heating has proved to be an ideal solution and the controllability and accuracy of the process make it of considerable interest for future work”.